Axle is in. Everything bolted up perfectly except the front driveshaft.
UPDATE SINCE INSTALL: Driveshaft was shortened 1.5 inches and fits perfectly.
As you can see, the drag link and track bar are at much better angles now.
Brakes work great. ABS is working :thumb: . Steering is tight but a little flighty around 45-50 (SINCE INSTALL: TURNED OUT CASTER WAS TOO LOW), I'll have to diagnose it as soon as I can. No real clearance issues but I will have to re-do something on the bump stops. When we cycled the axle, it appeared they would be perfect but back on the ground, they're not. They're hitting the upper control arm bolts. And I heard every hit on the test drive. Doesn't appear to be any bump steer, but I didn't have a lot of time to drive it tonight.
Here's some of the details. This is how I assumed the bump stops would work by building a platform right behind the track bar bracket. When I was all done tonight, I did notice the axle needs to move to the left about half inch, so once I fix that, it may work good. (EDIT, THIS DIDN'T WORK. BUMP STOP PAD FELL OFF AS IT SITS ON EDGE OF AXLE INSTEAD OF CENTERED ON AXLE. WORKING ON A WELD ON SOLUTION FOR THIS).
As far as the track bar, I had to shorten it about 5 inches. And now it looks like I'll have to shorten it another half inch or so. Luckily it is adjustable. After doing the string test, it appeared the best option for me at 4 inches of lift was to use the second hole down from the top on the track bar bracket (Clayton gives you 4) to keep the bar parallel with the drag link. I had to weld 12mm washers onto that hole because they are originally drilled out to big. I wanted to retain my factory sleeve and bolt size which is 12mm.
Track bar cut.
Track bar sleeved.
12mm washers welded on front and back. UPDATE: I used the 2nd hole down after a driving it a couple hundred miles which meant welding more washers.
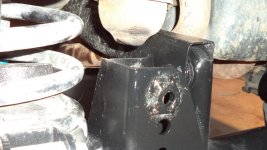