Memorial Day Monday my plan was to install the Rockstar skids :rock: and oil pan skid. I was doing some family stuff in the morning so I didn't get started until around 1pm. I figured the Rockstar skids :rock: would take a couple hours so I started with them. Good thing I did.
Everything started off fine. I jacked up the Jeep and got it on stands, removed the wheels and got started on the passenger side. Shock, sway bar link, and rear side of the LCA removed and out came the sawzall. It was my first time cutting through welds and even with a good new blade it's tough. I cut everything off and used the grinder to finish it up.
I went to slide the skid on but no way it was going on. I read in another thread about someone having the same problem and the issue is the LCA mount flares out slightly, but the skid does not have that flare. BFH time. I gave one side a bunch of whacks to remove the flare and the skid finally went on. Then there was an issue with one of the holes not lining up. So I got out the drill and made the one hole just large enough so the bolt would slide in. Ok, passenger side is good so I painted the exposed metal and moved to the driver's side while the paint dried.
I hadn't removed LCA on the driver's side yet and as soon as I did the whole axle rotated forward. FAK, I forgot about that! Oh well, thankfully I have a floor jack so I'll be able to jack up the pinion and reset the angle later. Same issues with installing the driver's side and same hole not lining up. Once I got it all done I painted it up and moved back to the passenger side.
I go to put the LCA back into the slot and it was tight, real tight. Now this is normally a good thing

, but not in this case. I beat the crap out of it with the rubber mallet but could not get the holes to line up. It's because I removed the flare in the LCA bracket now the metal sleeve (not sure what it's called) in the center of the CA joint was too long. After trying to work it from every angle my only option was to use the grinder and shave some metal off each side of the sleeve. I finally got it to go in and put everything back together, then did the driver's side. I put the wheels back on and let it settle then torqued all the bolts down.
It ended up taking 5 hours instead of 2 so I never got to the oil pan skid. Granted I did take a fair amount of time with a wet rag cleaning off the "dumb ass mud trip" I took a few weeks back! I won't be doing that again. Shit sucks to get off!
In the end, even though they were a pain in the ass, I'm glad I installed the skids. They should prove to be useful and I'm getting some much needed wrench time and learning along the way. Now I know to at least double my time estimates!
F*$king mud!!! :doh:
Much better!
Ain't gonna happen :grayno:
:rock:
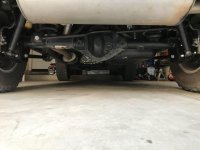