WJCO
Meme King
The question comes up from time to time about doing your own gears at home. Well, it can be done, but it is a big deal and very time-consuming. This is the first set of gears that I've ever done on the ground and it really is a pain in the ass. But if you have the proper tools, it can be done. This will be a semi-writeup that will cover the process but won't include everything. I did my best to take pictures along the way but likely didn't capture everything. If other members have tips and tricks, I certainly encourage posting those. This write-up will assume that new bearings are used. This write-up is not gospel, it is merely an attempt to show others what is truly involved in re-gearing. This is a very meticulous and time-consuming venture that requires patience, specialty tools, and constant questioning of why you started this to begin with at your house instead of paying a professional.
This writeup will not cover tool sizes, etc, it will only cover the process. Sorry. It will also not cover the removal of driveshafts, diff covers, nor axles. It is assumed if you are attempting to re-gear yourself, you already have that knowledge. If not, there are other threads for that. This will only cover gear setup.
Starting, make sure you have the proper OEM specifications and that your parts are correct. By counting the ring gear teeth and the pinion teeth, divide the two to make sure you were actually supplied with the correct gear ratio. As far as tools, you will need a press, some kind of bearing puller, an inch pound DIAL torque wrench, a dial indicator, a dial caliper, along with a full set of sockets and wrenches.
The first thing to do is to ensure your carrier cap bolts are marked. If not , mark them yourself. The caps are machined with the axle and on ours, the left side had a sideways 'A' and the right side had a proper linear 'A.' They have to go back in the EXACT same location.
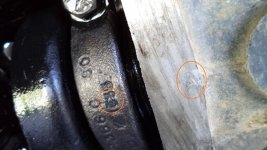
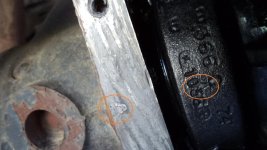
Loosen the caps but leave the bolts threaded into the housing a little. It may help to remove the carrier with a prybar and block of wood. It will be tight. Leaving the bolts and caps in place will prevent the heavy slippery carrier from accidentally falling on the floor. After the caps are removed, make sure the carrier preload shims are kept on the correct sides. If you are planning on re-using the carrier, the same shims will get you pretty close to a good starting point when you re-assemble.
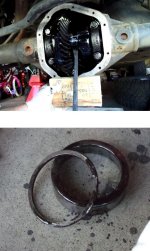
Sometimes the shims stick in the housing, keep an eye out for that.
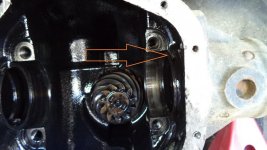
You should measure the shims and record the reading of both the left and right sides along with the total thickness of shims. If you are re-using the carrier, the total shim thickness of both sides will need to be accounted for. Once you do the gear setup, if you remove shims at all from one side, you need to add them to the other. This ensures the carrier bearings have the proper pre-load. If you are installing a locker (different carrier), the locker should come with instructions on what measurements need to be taken to set this up.
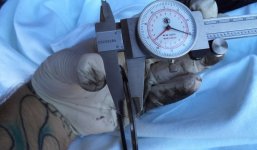
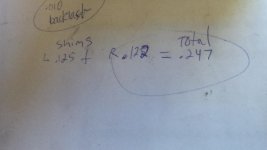
Once the carrier is removed, ensure that the bearings and races are indeed the correct parts.
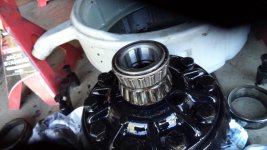
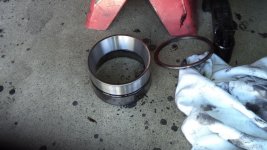
Put the carrier in the vice of your choice. Surround the carrier with thick rags or wood blocks and make sure it's tight. After removing the bolts, a light tap with a good sized hammer will remove the ring gear from the carrier.
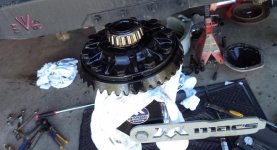
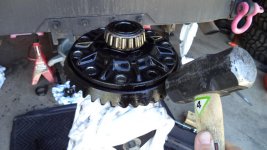
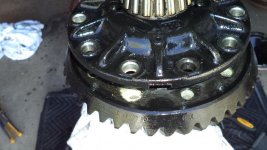
After the ring gear is removed, it's time to clean up the carrier, the new ring gear, and install the new ring gear to the carrier. Using a file, stone/sand the ring gear and carrier to ensure of no burrs or high spots. While this may sound ridiculous, it is important. I had two burrs on my carrier and ring gear while doing this today. Also use a sanding block to ensure all surfaces are clean and free of debris.
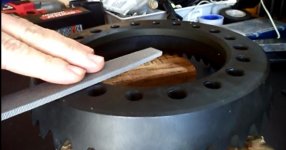
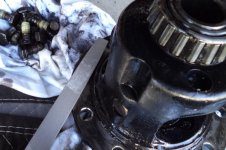
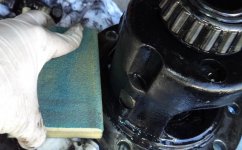
Note that some aftermarket gears have TWO different size bolt holes. Make sure that you check the bolts that came with the master install kit to ensure you are setting them in the right bore. The bolts that came with the master install kit will likely be the larger ones. If for some reason your carrier will not allow the bolts to pass through, you will need to re-drill your carrier to the correct size. This is not uncommon, but pay attention to it.
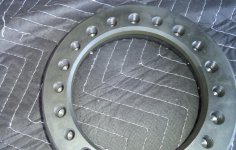
After cleaning the new ring gear and carrier, it should fit on normally by hand, however if it doesn't, DO NOT FORCE IT. You can put the ring gear in the oven at 170F for 20 minutes and expand it so it will fit on just fine.
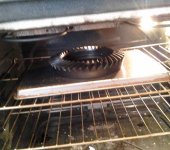
Make sure and locktite the ring gear bolts.
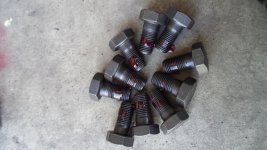
After the new ring gear is installed, make sure it is torqued to specs.
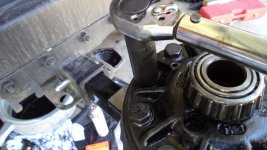
Now it's time to remove the carrier bearings and press the new ones on. If you can get ahold of a clamshell puller, it is fricking awesome and will save you a ton of time. You will need a high-powered impact to use it.
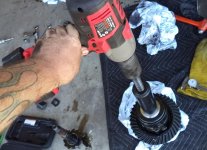
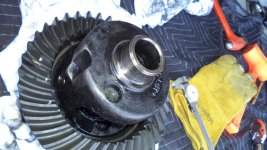
This writeup will not cover tool sizes, etc, it will only cover the process. Sorry. It will also not cover the removal of driveshafts, diff covers, nor axles. It is assumed if you are attempting to re-gear yourself, you already have that knowledge. If not, there are other threads for that. This will only cover gear setup.
Starting, make sure you have the proper OEM specifications and that your parts are correct. By counting the ring gear teeth and the pinion teeth, divide the two to make sure you were actually supplied with the correct gear ratio. As far as tools, you will need a press, some kind of bearing puller, an inch pound DIAL torque wrench, a dial indicator, a dial caliper, along with a full set of sockets and wrenches.
The first thing to do is to ensure your carrier cap bolts are marked. If not , mark them yourself. The caps are machined with the axle and on ours, the left side had a sideways 'A' and the right side had a proper linear 'A.' They have to go back in the EXACT same location.
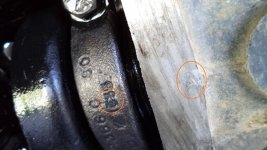
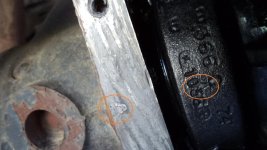
Loosen the caps but leave the bolts threaded into the housing a little. It may help to remove the carrier with a prybar and block of wood. It will be tight. Leaving the bolts and caps in place will prevent the heavy slippery carrier from accidentally falling on the floor. After the caps are removed, make sure the carrier preload shims are kept on the correct sides. If you are planning on re-using the carrier, the same shims will get you pretty close to a good starting point when you re-assemble.
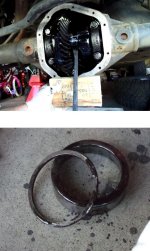
Sometimes the shims stick in the housing, keep an eye out for that.
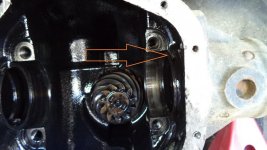
You should measure the shims and record the reading of both the left and right sides along with the total thickness of shims. If you are re-using the carrier, the total shim thickness of both sides will need to be accounted for. Once you do the gear setup, if you remove shims at all from one side, you need to add them to the other. This ensures the carrier bearings have the proper pre-load. If you are installing a locker (different carrier), the locker should come with instructions on what measurements need to be taken to set this up.
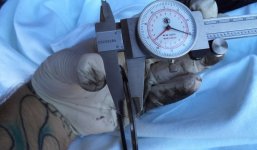
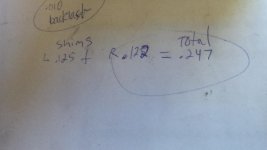
Once the carrier is removed, ensure that the bearings and races are indeed the correct parts.
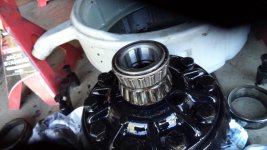
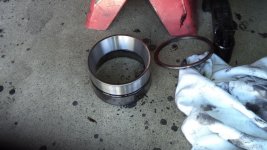
Put the carrier in the vice of your choice. Surround the carrier with thick rags or wood blocks and make sure it's tight. After removing the bolts, a light tap with a good sized hammer will remove the ring gear from the carrier.
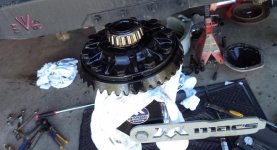
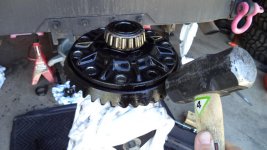
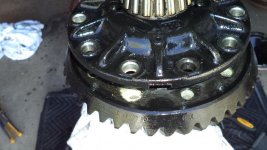
After the ring gear is removed, it's time to clean up the carrier, the new ring gear, and install the new ring gear to the carrier. Using a file, stone/sand the ring gear and carrier to ensure of no burrs or high spots. While this may sound ridiculous, it is important. I had two burrs on my carrier and ring gear while doing this today. Also use a sanding block to ensure all surfaces are clean and free of debris.
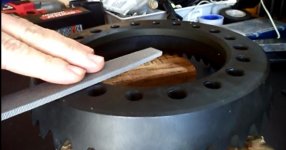
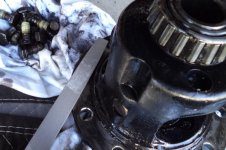
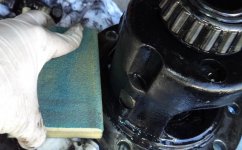
Note that some aftermarket gears have TWO different size bolt holes. Make sure that you check the bolts that came with the master install kit to ensure you are setting them in the right bore. The bolts that came with the master install kit will likely be the larger ones. If for some reason your carrier will not allow the bolts to pass through, you will need to re-drill your carrier to the correct size. This is not uncommon, but pay attention to it.
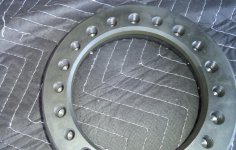
After cleaning the new ring gear and carrier, it should fit on normally by hand, however if it doesn't, DO NOT FORCE IT. You can put the ring gear in the oven at 170F for 20 minutes and expand it so it will fit on just fine.
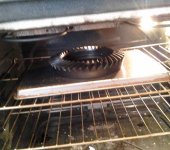
Make sure and locktite the ring gear bolts.
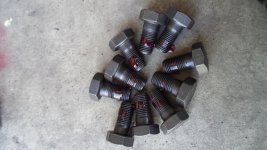
After the new ring gear is installed, make sure it is torqued to specs.
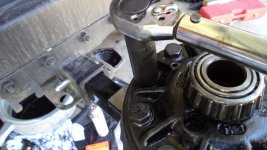
Now it's time to remove the carrier bearings and press the new ones on. If you can get ahold of a clamshell puller, it is fricking awesome and will save you a ton of time. You will need a high-powered impact to use it.
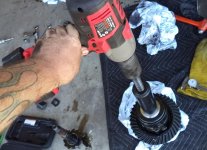
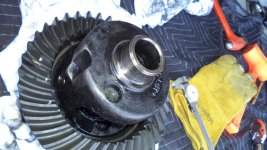
Last edited: