Disciple Off Road
Hooked
The other day, out of pure dumb luck, I happed to look at by PSC power steering pump and noticed my serpentine belt had slightly walked off of the pully and could see some black residue from the belt slightly rubbing somewhere. I tore into the Jeep and released the tension on the belt to remove it. I immediately noticed the power steering pump move/pivot a good amount and knew we had a problem.
This is on a 2014 Jeep JK Rubicon and installed this full PSC hydro assist kit approximately 5 years ago. I have had absolutely zero issues with it and still did not notice any unusual noise or performance issues. Knowing I had an issue and having OCD, I just ordered a new pump and a new bracket as I already new I had an older version.
After Removing the belt, high pressure line and return line, I was really able to see just how bad this was which you can see in this short clip.
After removing the pump with the bracket, I noticed two of the four bolt heads were missing with the threads of the bolts still inside. (one of the bolt heads fell out as I pulled the pump). This is a two piece bracket. As I began to remove the high pressure line fitting on the old pump, the last bolts holding the bracket together broke. Needless to say, I couldn't have caught this at a better time and avoided a really bad day.
The bracket that was included with my original kit was the older style and should note that PSC has since updated the bracket which they weld on both sides along with four bolts. So if you recently installed a PSC kit, you should have the updated bracket.
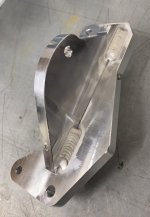
All better
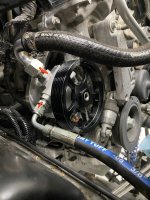
Note: This is also a good time to check and change your idler pulleys if needed.
PSC makes a great product and is great to see that they recognized and addressed this issue. If you have or think you might have the older style bracket, definitely something to keep an eye on to prevent a failure. The new bracket is a direct replacement if you decide to change yours from the older style.
Hope this helps!
This is on a 2014 Jeep JK Rubicon and installed this full PSC hydro assist kit approximately 5 years ago. I have had absolutely zero issues with it and still did not notice any unusual noise or performance issues. Knowing I had an issue and having OCD, I just ordered a new pump and a new bracket as I already new I had an older version.
After Removing the belt, high pressure line and return line, I was really able to see just how bad this was which you can see in this short clip.
After removing the pump with the bracket, I noticed two of the four bolt heads were missing with the threads of the bolts still inside. (one of the bolt heads fell out as I pulled the pump). This is a two piece bracket. As I began to remove the high pressure line fitting on the old pump, the last bolts holding the bracket together broke. Needless to say, I couldn't have caught this at a better time and avoided a really bad day.
The bracket that was included with my original kit was the older style and should note that PSC has since updated the bracket which they weld on both sides along with four bolts. So if you recently installed a PSC kit, you should have the updated bracket.
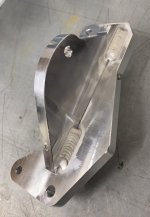
All better
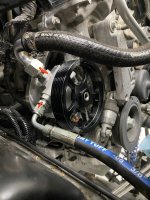
Note: This is also a good time to check and change your idler pulleys if needed.
PSC makes a great product and is great to see that they recognized and addressed this issue. If you have or think you might have the older style bracket, definitely something to keep an eye on to prevent a failure. The new bracket is a direct replacement if you decide to change yours from the older style.
Hope this helps!