professorkx
New member
Starting a build on a 1978 CJ5. This jeep is already a great rock crawler with 304, T18 Ford 4 speed, clocked dana 20, tom woods shafts, slight lift on leaf springs, lockers front and rear and more.
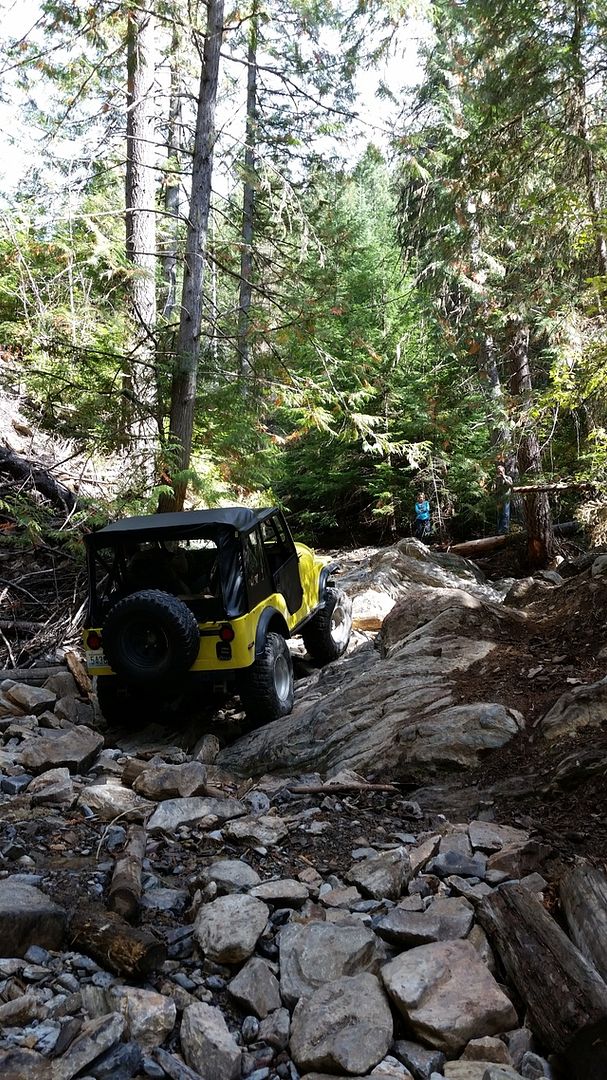
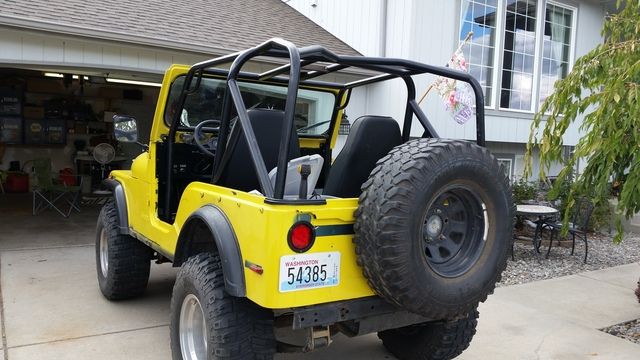
The jeep is going to my youngest son who is a disabled vet who broke his back serving our country, so needs a ride that is much better than leaf springs will ever deliver. The build plan includes changing the suspension to the a long arm using parts from Genright and King coil over shocks, moving the front axle as far forward as possible and the rear as far back as possible. The front will be a 3-link with track bar, while the rear will be a 4-link. The jeep needs to be road worthy and street legal, so we are limited on our mods.
My son and I got started last weekend, put the jeep on stands, removed the 35 inch tires and pulled off the old leaf spring system.
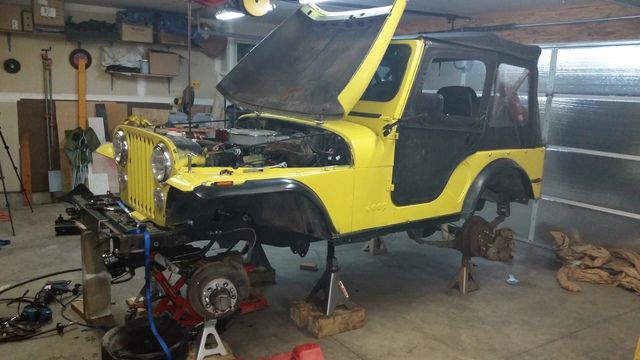

Next up was to move the steering box forward as far as possible, as this will dictate how far I can move the front axle forward. The tires can't go forward past the front bumper so he isn't hassled by LEO, but I am hoping for at least 5 inches. In the picture below, the box has been moved forward 4.5 inches, but with pitman arm modifications to yield 5.5 inches on center instead of 6.75 inches, I am going to be close.
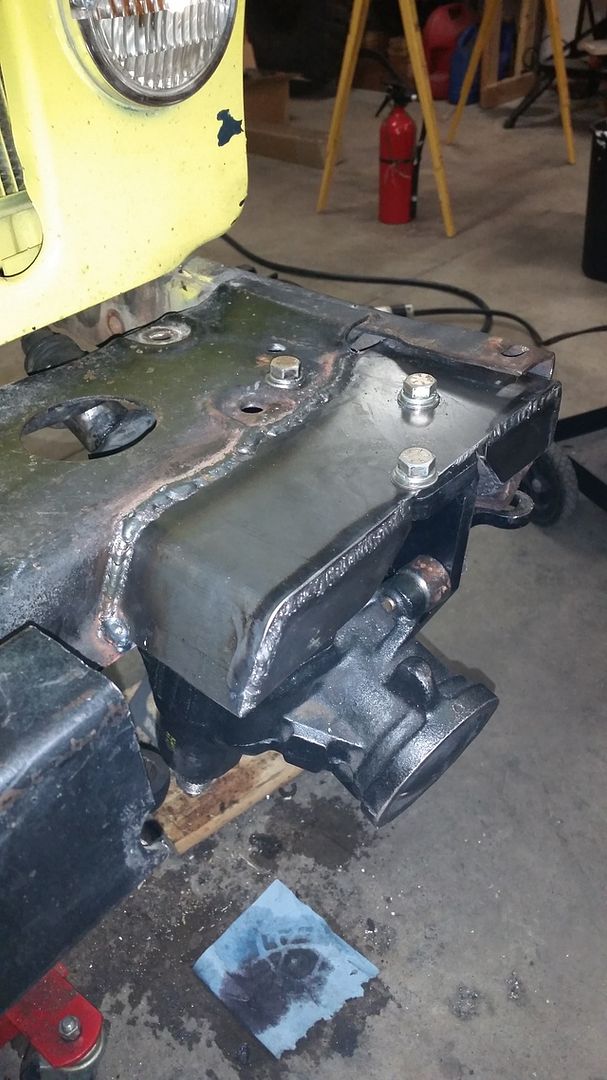
Unfortunately, I had previously flipped the tie rod and drag link, but the frame is too low with the axle moved forward to get full travel, so they have to go back to the original spot. Might mean we have to buy new tie rod and drag link with heim joints, but hoping we can make the stock parts works to save some money.
UPS showed up with the king shocks today, so I am hoping to get the front axle arms at least spot welded in place, as well as the shock hoop. This will help determine if I need to notch the frame to allow the shocks to move on full flex.
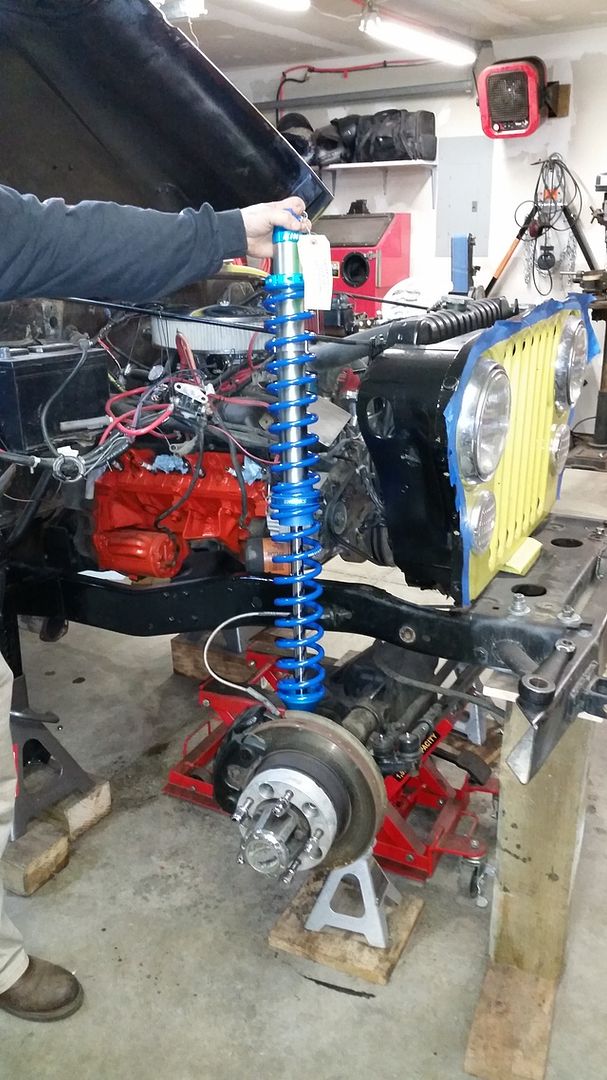
I will complete the front before moving to the rear to ensure we don't have too many things going at once. I will have to shorten the passengers side header 3 inches to have room for the top link, but stock manifolds are a backup plan. The rear frame will need to be notched for shocks, and the shocks will go into the bed of the jeep, so a new gas tank will need to be fabricated.
More pictures to come as progress continues...
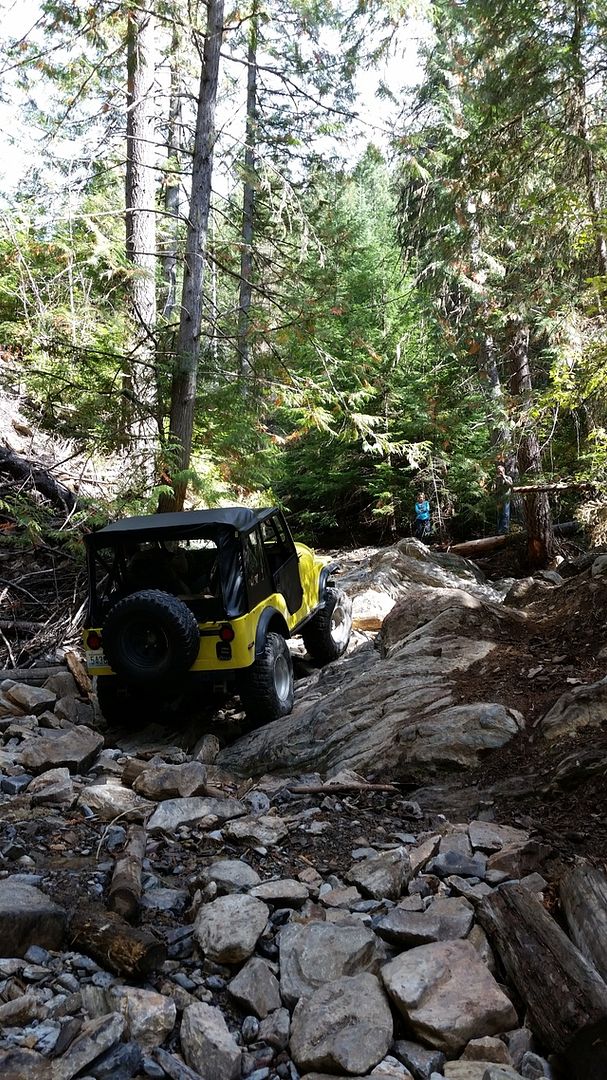
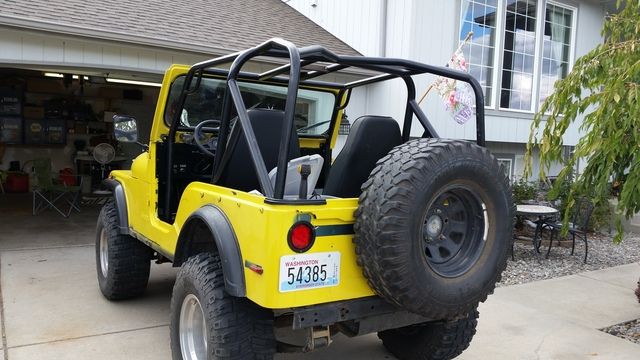
The jeep is going to my youngest son who is a disabled vet who broke his back serving our country, so needs a ride that is much better than leaf springs will ever deliver. The build plan includes changing the suspension to the a long arm using parts from Genright and King coil over shocks, moving the front axle as far forward as possible and the rear as far back as possible. The front will be a 3-link with track bar, while the rear will be a 4-link. The jeep needs to be road worthy and street legal, so we are limited on our mods.
My son and I got started last weekend, put the jeep on stands, removed the 35 inch tires and pulled off the old leaf spring system.
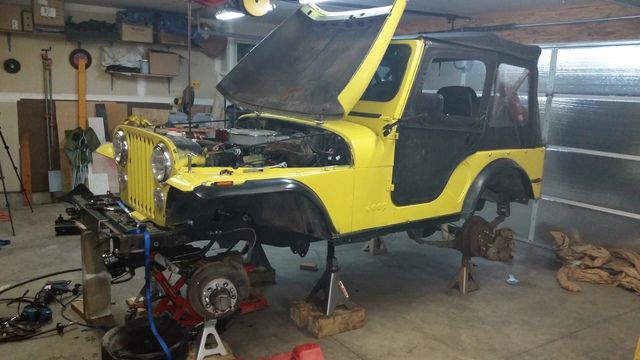

Next up was to move the steering box forward as far as possible, as this will dictate how far I can move the front axle forward. The tires can't go forward past the front bumper so he isn't hassled by LEO, but I am hoping for at least 5 inches. In the picture below, the box has been moved forward 4.5 inches, but with pitman arm modifications to yield 5.5 inches on center instead of 6.75 inches, I am going to be close.
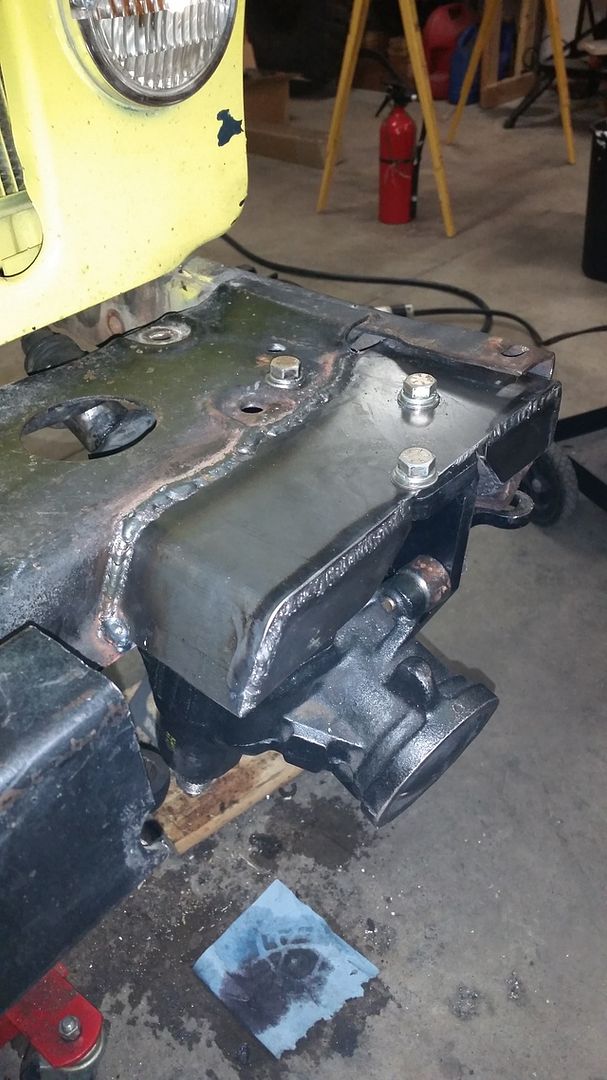
Unfortunately, I had previously flipped the tie rod and drag link, but the frame is too low with the axle moved forward to get full travel, so they have to go back to the original spot. Might mean we have to buy new tie rod and drag link with heim joints, but hoping we can make the stock parts works to save some money.
UPS showed up with the king shocks today, so I am hoping to get the front axle arms at least spot welded in place, as well as the shock hoop. This will help determine if I need to notch the frame to allow the shocks to move on full flex.
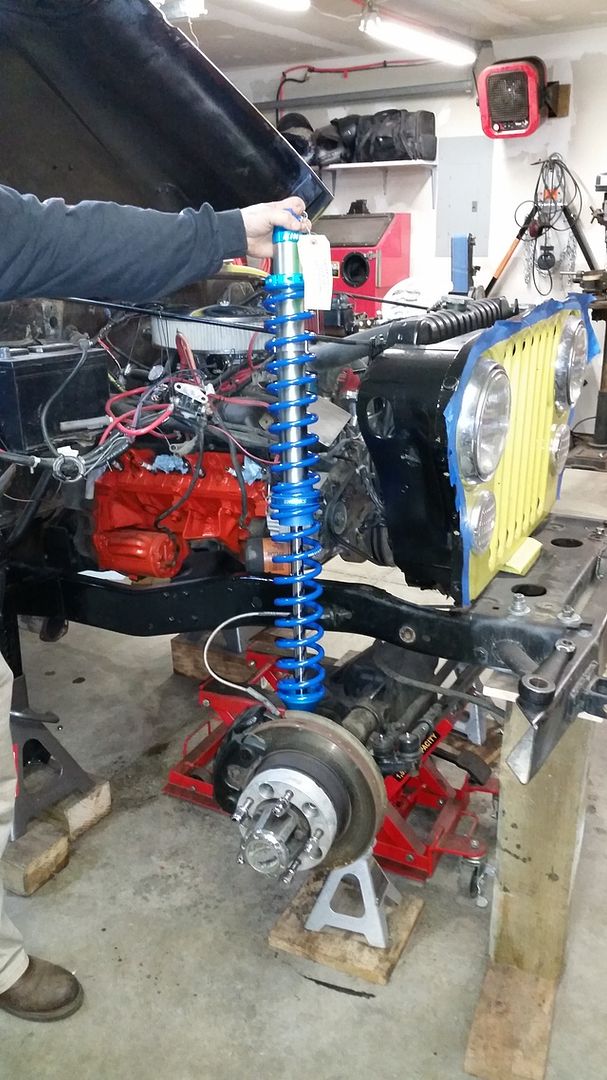
I will complete the front before moving to the rear to ensure we don't have too many things going at once. I will have to shorten the passengers side header 3 inches to have room for the top link, but stock manifolds are a backup plan. The rear frame will need to be notched for shocks, and the shocks will go into the bed of the jeep, so a new gas tank will need to be fabricated.
More pictures to come as progress continues...